PCB Rework
After the PCBA inspection is completed, the defective PCBA needs to be repaired. The company has two methods for repairing the SMT PCBA.
One is to use a constant temperature soldering iron (manual welding) for repair, and the other is to use a repair workbench (hot air welding) for repair. No matter which method is adopted, it is required to form a good solder joint in the shortest time.
Therefore, when using a soldering iron, it is required to complete the soldering point in less than 3 seconds, preferably about 2 seconds.
The diameter of the solder wire requires priority to use diameter φ0.8mm, or use φ1.0mm, not φ1.2mm.
Soldering iron temperature setting: normal welding wire to 380 gear, high temperature welding wire to 420 gear.
Ferrochrome rework method is manual welding
1. Treatment of the new soldering iron before use:
The new soldering iron can be used normally after the soldering iron tip is plated with a layer of solder before use. When the soldering iron is used for a period of time, an oxide layer will be formed on and around the blade surface of the soldering iron tip, which will cause difficulty in "eating tin". At this time, the oxide layer can be filed, and solder can be re-plated.
2. How to hold the soldering iron:
Reverse grip: Use five fingers to hold the handle of the soldering iron in your palm. This method is suitable for high-power electric soldering irons to weld parts with large heat dissipation.
Ortho-grip: Hold the handle of the soldering iron with four fingers except the thumb, and press the thumb along the direction of the soldering iron. The soldering iron used in this method is also relatively large, and most of them are curved soldering iron tips.
Pen holding method: holding an electric soldering iron, like holding a pen, is suitable for low-power electric soldering irons to weld small parts to be welded.
3. Welding steps:
During the welding process, the tools should be placed neatly, and the electric soldering iron should be firmly aligned. Generally, it is best to use tube-shaped solder wire with rosin for soldering. Hold the soldering iron in one hand and the solder wire in the other.
Clean the soldering iron tip Heat the soldering point Melt the solder Move the soldering iron tip Remove the soldering iron
① Quickly touch the heated and tinned soldering iron tip to the cored wire, then touch the solder joint area, use the molten solder to help the initial heat transfer from the soldering iron to the workpiece, and then move the solder wire away to contact the soldering The surface of the soldering iron tip.
②Contact the soldering iron tip to the pin/pad, and place the soldering wire between the soldering iron tip and the pin to form a thermal bridge; then quickly move the soldering wire to the opposite side of the soldering area.
However, it is usually caused by improper temperature, excessive pressure, extended retention time, or damage to the PCB or components caused by the three together.
4. Precautions for welding:
The temperature of the soldering iron tip should be appropriate. Different temperature soldering iron tips will produce different phenomena when placed on the rosin block. Generally speaking, the temperature when the rosin melts faster and does not emit smoke is more suitable.
The soldering time should be appropriate, from heating the solder joint to the solder melting and filling the solder joint, generally should be completed within a few seconds. If the soldering time is too long, the flux on the solder joints will completely volatilize, and the fluxing effect will be lost.
If the soldering time is too short, the temperature of the soldering point will not reach the soldering temperature, and the solder will not melt sufficiently, which will easily cause false soldering.
The amount of solder and flux should be used appropriately. Generally, the use of too much or too little solder and flux on the solder joint will have a great impact on the quality of soldering.
To prevent the solder on the solder joint from flowing randomly, the ideal soldering should be that the solder is only soldered where it needs to be soldered. In the soldering operation, the solder should be less at the beginning. When the soldering point reaches the soldering temperature and the solder flows into the gap of the soldering point, the solder will be refilled to complete the soldering quickly.
Do not touch the solder joints during the soldering process. When the solder on the solder joints has not completely solidified, the soldered devices and wires on the solder joints should not be moved, otherwise the solder joints will be deformed and virtual welding will occur.
Do not scald the surrounding components and wires. When soldering, be careful not to scald the plastic insulation layer of the surrounding wires and the surface of the components, especially for products with compact welding structures and complex shapes.
Do the cleaning work after welding in time. After the welding is completed, the cut wire head and the tin slag dropped during welding should be removed in time to prevent hidden dangers from falling into the product.
5. Treatment after welding:
After welding, you need to check:
Whether there is missing solder.
Is the gloss of the solder joints good?
The solder joint is insufficient.
Whether there is residual flux around the solder joints.
Whether there is continuous welding.
Whether the pad has fallen off.
Whether there are cracks in the solder joints.
Is the solder joint uneven?
Whether the solder joints are sharp.
Pull each component with tweezers to see if there is any looseness.
6. Desoldering:
When the soldering iron tip is heated by the desoldering point, as soon as the solder melts, the lead of the component should be pulled out in the direction perpendicular to the circuit board in time. Regardless of the installation position of the component, whether it is easy to take out, do not force or twist the component. So as not to damage the circuit board and other components.
Do not use excessive force when desoldering. The practice of prying and shaking the contact with an electric soldering iron is very bad. Generally, the contact is not allowed to be removed by pulling, shaking, twisting, etc.
Before inserting a new component, the solder in the pad wire hole must be cleaned, otherwise the pad of the circuit board will be warped when inserting the lead of the new component.
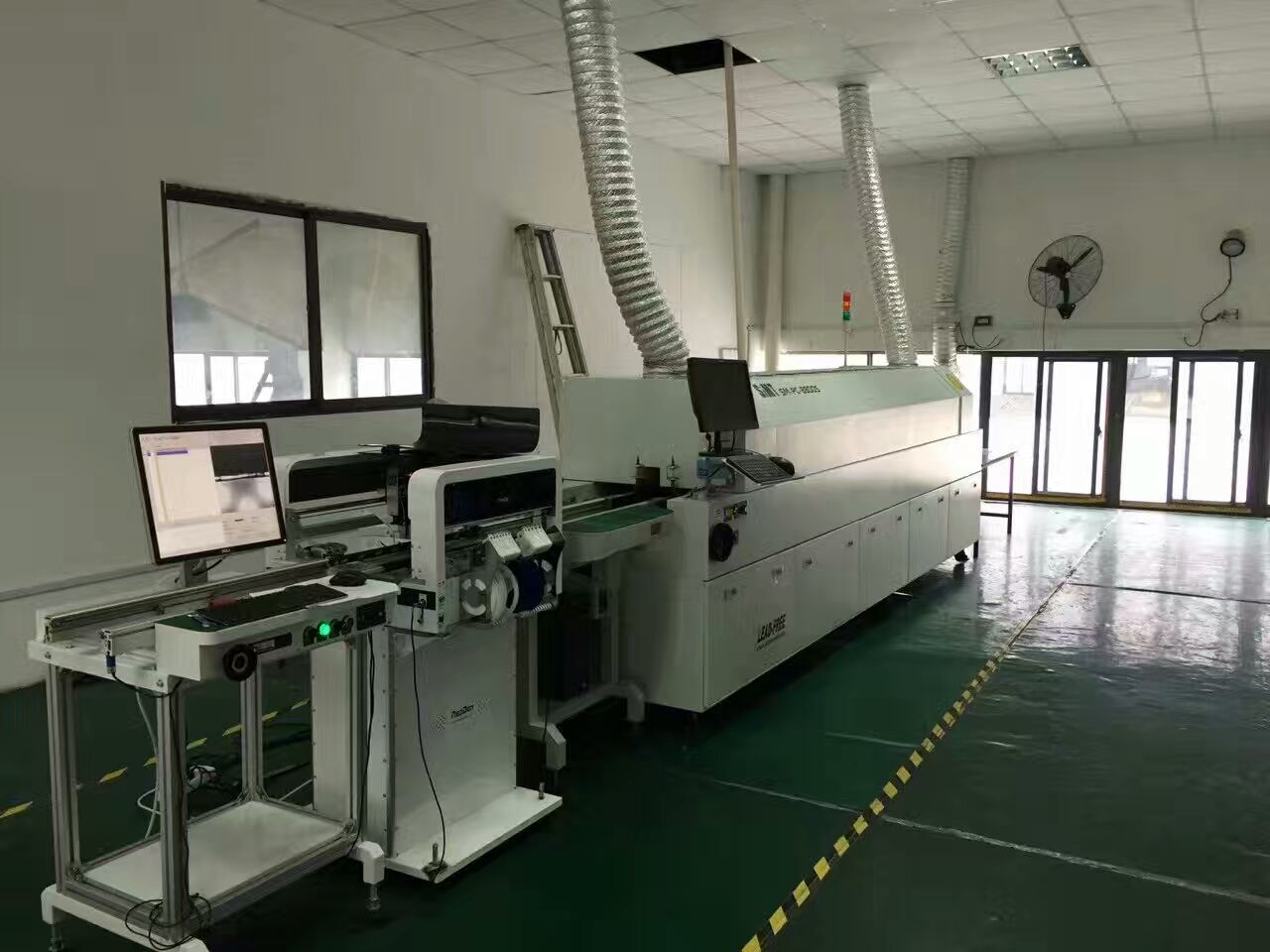
NeoDen provides a full SMT assembly line solutions, including SMT reflow oven, wave soldering machine, pick and place machine, solder paste printer, PCB loader, PCB unloader, chip mounter, SMT AOI machine, SMT SPI machine, SMT X-Ray machine, SMT assembly line equipment, PCB production Equipment SMT spare parts, etc any kind SMT machines you may need, please contact us for more information:
Post time: Jul-22-2020